Dr Mayo Adetoro is a Senior Lecturer in Mechanical and Aerospace Engineering at Brunel University London, and Dr James Campbell is a Reader in Structural Engineering at Brunel University London.
Nasa’s space shuttle operated in low-Earth orbit for 30 years before its retirement in 2011. However, the US space agency’s replacement for this vehicle, Orion, returned to the conical capsule design familiar from the Apollo missions. This was because Nasa intended that this newer craft be used for exploring targets in deep space, such as the Moon.
But in recent years, we have seen a return of the spaceplane design. Since 2010, the US Space Force (and formerly the US Air Force) has been launching a robotic spaceplane called the X-37B into low Earth orbit on classified missions. China has its own military spaceplane called Shenlong.
This year could see a test flight of the company Sierra Space’s Dream Chaser – the first commercial spaceplane capable of orbital flight. If all goes well, the vehicle could be used to resupply the International Space Station (ISS) with cargo and, eventually, crew.
Spaceplanes can fly or glide in the Earth’s atmosphere and land on runways rather than using parachutes to land in water or flat ground like capsules. They’re also more manoeuvrable as the spacecraft reenters the atmosphere, increasing the area of the Earth’s surface where landing is possible from a specific re-entry point.
Spaceplanes also allow a gentler but longer flight path during re-entry and a softer landing, which is easier on crew and cargo than capsules, which can land with a thump. A runway also allows ground support crews and infrastructure to be ready at the landing location.
Cost and complexity
But spaceplanes are more complex and heavier than an equivalent capsule. The winged body shape poses a particular challenge for designing thermal protection systems (TPS) – the heat-resistant materials that protect the craft from scorching temperatures on re-entry. These additional costs mean it’s impractical to design a spaceplane for a single flight. They need to be used again and again to be viable.
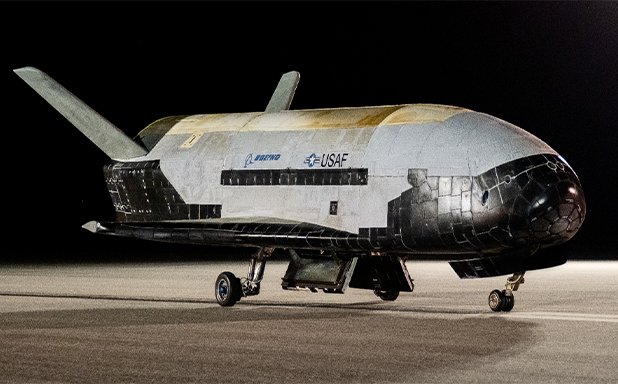
The US Space Force’s X-37B carries no crew, and its missions are classified (c) US Space Force
There has been interest in spaceplanes from the earliest days of human spaceflight. A military spaceplane project called Dyna-Soar was started in the US in 1957, then cancelled just after construction started. The vehicle was sophisticated for its time, built using a metal alloy that is able to withstand high temperatures and featuring a heat shield on the front that could be detached after it returned from space, so that the pilot could see clearly as he was landing.
The space shuttle, which entered service in 1981, was the first operational spaceplane. It was supposed to launch more often than it did and have greater reusability but it turned out that extensive refurbishment was required between launches. It did, however, demonstrate the ability to return astronauts and large cargo from orbit.
Other space agencies invested in the 1980s and 1990s, in Europe, with the Hermes spaceplane, and Japan, with the HOPE vehicle. Both programmes were cancelled in large part because of cost. The Soviet Union developed its own shuttle-like vehicle called Buran, which successfully flew to space once in 1988. The programme was cancelled after the collapse of the Soviet Union.
Feeling the heat
Spaceplanes have specific requirements for the final part of their journeys – as they return from space. During atmospheric re-entry, they are heated to over one thousand degrees Celsius as they travel at hypersonic speeds of over seven kilometres per second – more than 20 times the speed of sound. A blunt nose design (where the edge of the spacecraft is rounded) is an ideal shape because it reduces build-up of heat at the foremost part of the vehicle.
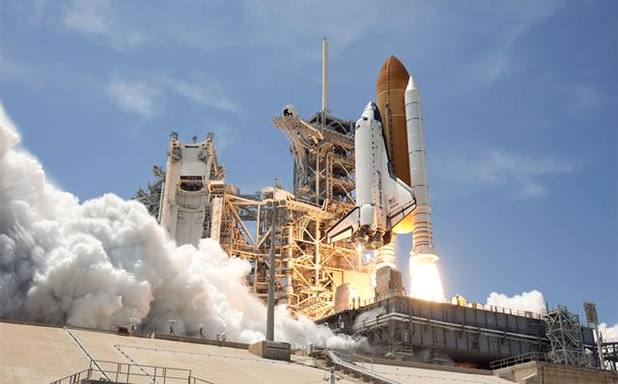
The launch of Space Shuttle Atlantis (c) NASA
Even so, the expected temperatures experienced by the craft can still be as high as 1600°C, necessitating a thermal protection system on the outside of the vehicle. The space shuttle TPS included ceramic tiles that were especially heat resistant and a reinforced carbon-carbon matrix that was capable of withstanding temperatures as high as 2400°C.
The loss of the Columbia shuttle during re-entry in 2003, causing the deaths of seven astronauts, was the result of a breach in the TPS on the leading edge of the wing. This resulted from a piece of insulating foam flying off the shuttle’s external tank during Columbia’s launch and hitting the wing.
This foam issue was recurrent with the shuttle because of the way it launched on the side of the external propellant tank. But newer spaceplane designs will fly atop conventional rockets, where falling foam isn’t a problem.
An effective TPS remains vital for the future success of spaceplanes, as are systems that monitor the TPS performance in real time.
Current vehicles
There are currently two operating spaceplanes, one Chinese and one American, that can reach orbit. Little information is available on China’s Shenlong, but the US military’s X-37B is better known. Weighing close to five tonnes at launch, the nine metre-long, uncrewed vehicle is launched using a conventional rocket and lands autonomously on a runway at the end of its mission.
The X-37B’s TPS uses tiles similar to the shuttle over the lower surface with a lower-cost alternative to reinforced carbon-carbon called Tufroc, developed for the X37B, on the nose and leading edges.
They should soon be joined by Dream Chaser, which was was developed by the company to carry both cargo and astronauts, but Nasa wants to prove its safety before carrying people by using it to carry cargo to the space station first. The ability to return comparatively fragile cargo to the surface because of a softer landing is a key capability. The tiles that protect Dream Chaser are made from silica, and each has a unique shape matched to the area on the vehicle they are designed to protect.
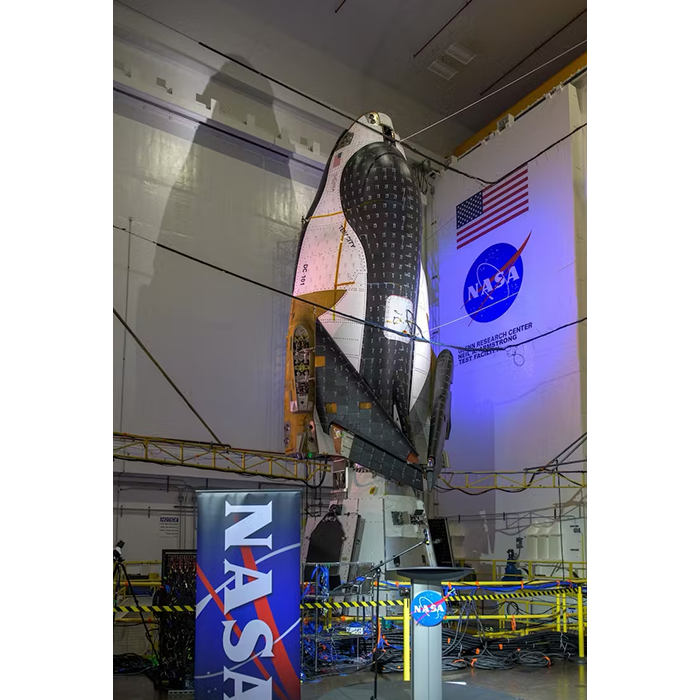
Dream Chaser in Feb 2024 (c) NASA
Future developments
There is continued interest in spaceplanes because of their ability to return crew and cargo to a runway. The demand for this capability is limited now. But if the costs of launching to space continue falling and an expansion of industry in space raises demand, they will become an increasingly viable alternative to capsules.
Longer term, there is also potential for spaceplanes capable of reaching orbit after taking off from a runway. The challenges of developing these single-stage-to-orbit (SSTO) vehicles is considerable. However, concepts such as the Skylon vehicle are leading to technical developments that could eventually support development of an SSTO craft.
For the foreseeable future, spaceplanes look promising for the following reasons: new design techniques, improved materials for the TPS, advanced computer modelling and simulation tools for optimising different aspects of design and flight parameters and continuous improvements in propulsion systems.
Given that several governments, space agencies, and private companies worldwide are investing heavily in spaceplane research and development, we could see a future where flights with these vehicles become routine.
This article is republished from The Conversation under a Creative Commons license. Read the original.
Reported by:
Press Office,
Media Relations
+44 (0)1895 26867
press-office@brunel.ac.uk