Engineering experts at Brunel University London won the Wild Card award at The Engineer Magazine’s annual Collaborate to Innovate Awards (C2I) on 29 February for their collaboration with industry on the EMPHASIZING project – a sustainable and cost-effective project committed to recycling glass fibres for the future production of cars and vehicles.
Now in its eighth year, the C2I Awards celebrate the UK’s most innovative and inspiring collaborative engineering projects and highlight how engineers are using their expertise and emerging technologies to solve some of the world’s biggest challenges.
The awards recognise the importance of the circular economy, which is a model of production that involves extending the life of materials by reusing and recycling them to reduce waste.
The Brunel Composites Centre (BCC), a research centre in Brunel’s College of Engineering, Design and Physical Sciences, is one of the collaborators on the award-winning project, and some of the team attended the awards ceremony at the Institution of Civil Engineers in Westminster.
The centre’s expert researchers specialise in transferring academic knowledge on composites materials – materials made up of two or more materials with different chemical properties – that can be practically applied to the automotive industry, aerospace industry and oil and gas industry.
BCC's research has been integral to the EMPHASIZING project, which started in 2022, in partnership with Ford UK, B&M Longworth, Gestamp, Gen 2 Plank Ltd, TWI and EMS Grivory to recycle glass fibre reinforced plastic (GFRP) that is currently going to landfill or being incinerated.
GFRP makes up the majority of the global £54.5 billion composites market, and the construction, infrastructure and transport sectors are all large-scale users, accounting for 70% of the one-million-plus tonnes produced annually in Europe alone.
“The increased use of glass fibres has led to concerns over how they are disposed of as waste,” said Dr Nithin Jayasree, a senior research fellow and team leader at BCC.
“There is a need for GFRP to be recycled cost-effectively and with a minimal environmental impact, which is what the EMPHASIZING project sets out to address,” he said.
“In addition to the generated waste, the wind energy sector is expected to decommission 40,000 to 60,000 tonnes of composite wind blade material over the next two years, further adding to the amount of GFRP waste.”
The project is developing a way to recycle and exploit these waste materials for future use within the automotive sector.
“We use an emerging recycling technology called DEECOM® to recover high-quality, clean, reusable glass fibres that are free from residues and have a retained length and properties akin to virgin materials,” said Dr Jayasree.
“The fibres are chopped into 6-mm lengths before a range of sizing chemistries are considered as part of ‘emphasizing’.
“It creates a new advanced material called glassene, which can be upcycled to achieve increased performance properties much higher than glass but at a similar cost.”
The C2I award follows the project’s Circularity and Recycling Award, which the team scooped at last month’s JEC Composites Innovation Awards.
The JEC Awards highlight the most successful and innovative collaborative projects in the composites industry internationally, and some of the EMPHASIZING team celebrated the win at a special award winners’ event in Paris earlier this week.
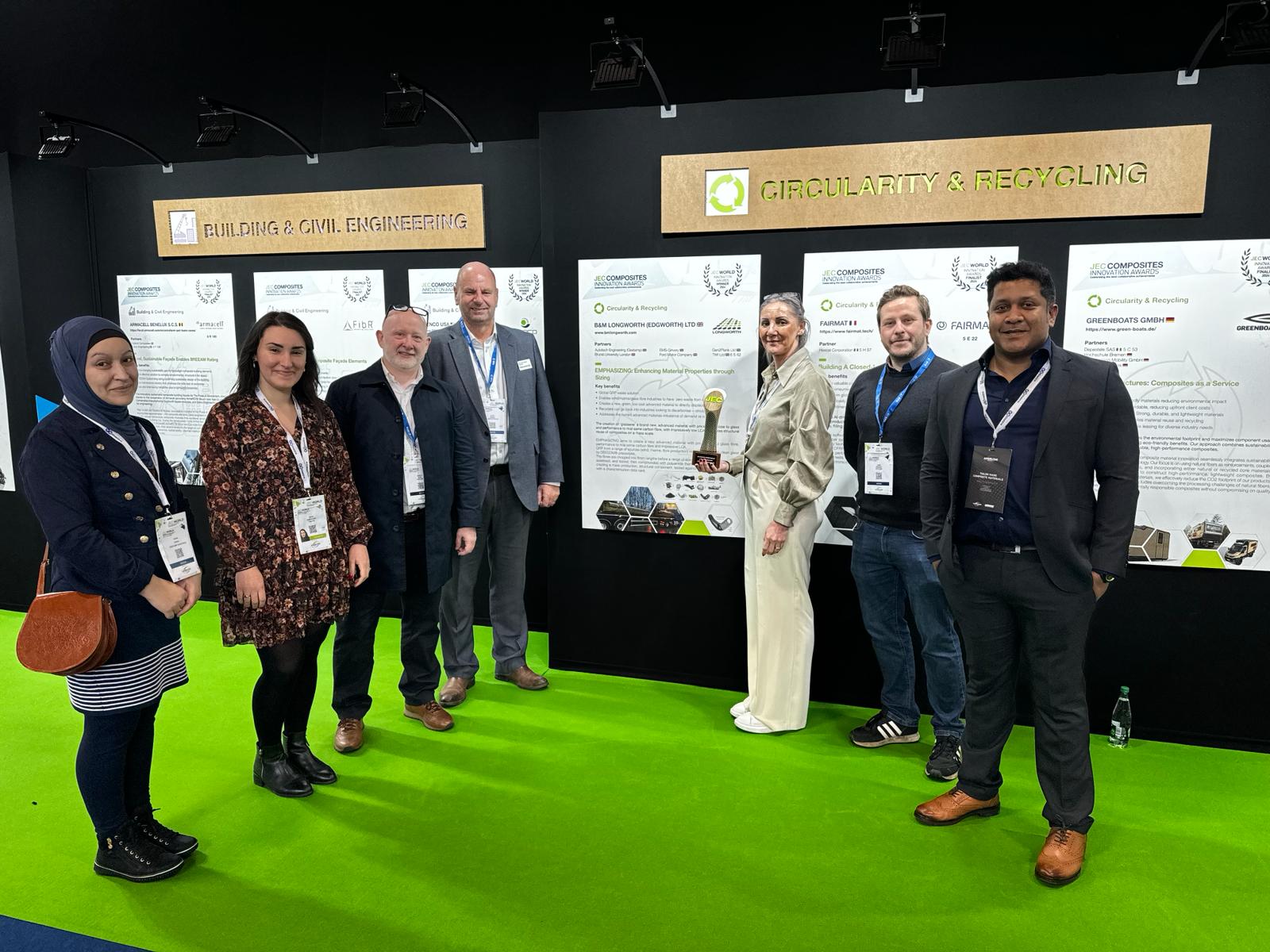
Dr Nithin Jayasree with some of the EMPHASIZING team at the JEC award winners' event in Paris
Brunel highly values its partnerships with industry, and BCC is delighted to be able to share its research and knowledge with the project partners.
“We are proud to be a part of the EMPHASIZING project and to receive industry recognition from the C2I Awards and the JEC Composites Innovation Awards,” said Dr Jayasree.
“We are committed to recycling composite materials as part of the project, and our main priorities have always been protecting the environment, sustainability and keeping costs low.
“Glassene will enable a sustainable future for composites, and it will become a first-choice material for the automotive industry as they increase their composite use from 2030.”
A special mention to Hesam Badriopens new window and Dr Saeid Dashatanopens new window from Brunel Composites Centre (BCC)opens new window who are currently working on the technical delivery of the project, and to Dr Sadik Omairey and Dr Mihalis Kazilas for their ongoing support with the project and for making an impact in the composite sector.
Reported by:
Nadine Palmer,
Media Relations
+44 (0)1895 267090
Nadine.palmer@brunel.ac.uk