In more than 4,000 m2 of laboratory space, and with over £43m of capital investment, BCAST has a unique range of facilities to carry out metallurgical research across the full range of Technology Readiness Levels (TRLs), from atomic level fundamental research to alloy and technology developments and on through to industrial applications.
Along with an array of laboratory scale equipment for fundamental research, BCAST’s purpose-built Advanced Metals Casting Centre (AMCC) and Advanced Metals Processing Centre (AMPC) house pilot and commercial scale metal casting and processing equipment to act as a unique scale-up facility. The AMCC and AMPC support our industrial partners to bridge the gap between fundamental, laboratory-scale research and full industrial trials, and to scale laboratory developed technologies to production demonstrators thus shortening the time to bring new technologies to market.
Casting and metal processing is fully supported by a comprehensive array of materials characterisation techniques including state-of-the-art instruments in advanced electron microscopy and analysis in our brand new Future Metallurgy Centre.
Fundamental and industrial research is complemented by computer modelling and simulation at all length scales, with a dedicated computer cluster running a broad range of packages.
All of our facilities are available for collaborative R&D. If you are interested in working with us, please either contact individual members of academic staff directly or contact Dr Mark Jones (BCAST Head of Business Development).
We also offer paid technical services.
Metal Casting
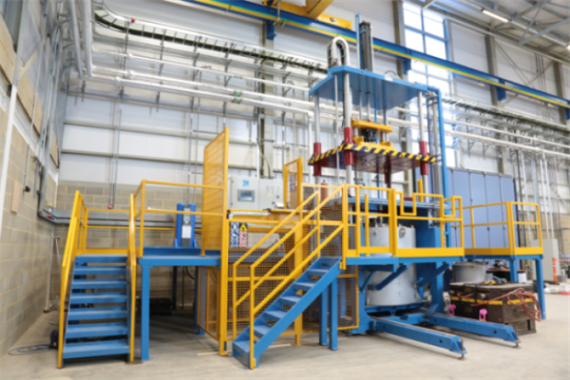
· 450 tonne vacuum assisted cold chamber HPDC
· 1600 tonne vacuum assisted cold chamber HPDC
· 24 tonne LPDC machine
· Tilting gravity die casting system
· No-bake sand casting line
· Direct chill casting unit capable of casting billets of 205 mm diameter and 2 m length
· Twin roll casting (TRC) units for Al and Mg strip
· A range of laboratory scale casting facilities and analysis (e.g. cooling curves, reduced pressure testing, TP1, etc.)
Metal Processing
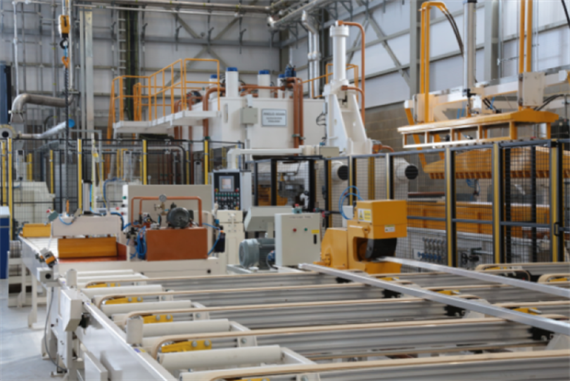
· 1600 tonne Al extrusion line
· 3D Freeform bending machine
· Electro-magnetic pulse forming-welding machine
· Small scale rolling mill
· Cold metal transfer welding
· Flowdrill fastening
· Self-piercing riveting
· Heat treatment furnaces
· Machining facilities: CNC turning and milling, and EDM wire cutting
Materials Characterisation
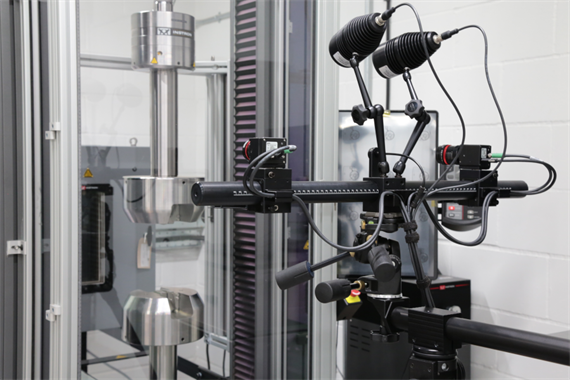
· Yxlon Y.CT Compact for component scale (macro) X-ray CT scanning
· Zeiss Xradia 410 Versa high resolution (micro) X-ray CT scanning
· GOM 3D Metrology system
· Uniaxial tensile testing (room and elevated temperatures)
· Fatigue testing (room and elevated temperatures)
· Differential scanning calorimetry and flash DSC
· Optical emission spectroscopy
· Gleeble 3800-GTC thermomechanical simulation system
Advanced Microscopy & Analysis
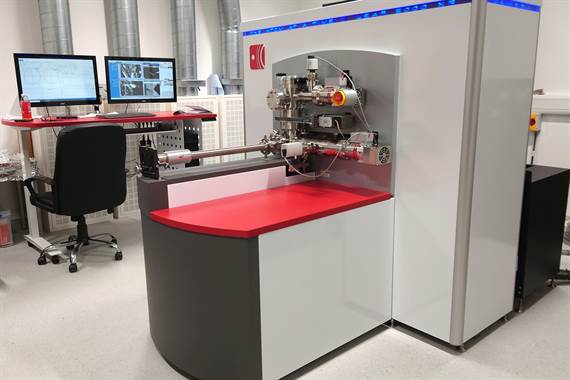
· Thermo Fisher Spectra 300 Cs-corrected S/TEM
· Thermo Fisher Talos F200i S-FEG TEM (with EDS, STEM imaging, HAADF)
· Zeiss Crossbeam FIB SEM
· Thermo Fisher Apreo 2 S HiVac SEM (with EDS, EBSD and in-chamber serial block-face ultramicrotome)
· Cameca LEAP 5000 XR atom probe
· Bruker D8 Discover XRD for phase ID, stress and texture measurements (room and elevated temperatures)
Modelling & Simulation
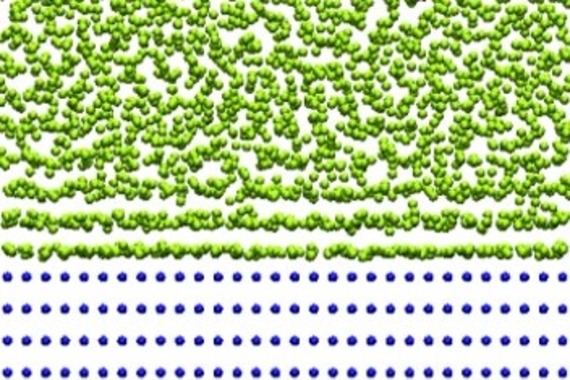
· Dedicated cluster computing facility: 800+ cores (Intel® Xeon® CPU E5-2680 v4 @ 2.40 GHz)
· Casting simulation: ProCAST, FLOW-3D, MAGMA
· Forming simulation: DEFORM
· FEA/CFD: ANSYS (Fluent and Mechanical), ABAQUS, OpenFOAM
· Microstructure simulation: MICRESS
· Thermodynamic modelling: PANDAT, Thermo-Calc
· DFT and atomistic: VASP, DL_POLY and LAMMPS
· Development tools: Intel® Parallel Studio XE Professional Edition for Fortran and C++ Windows